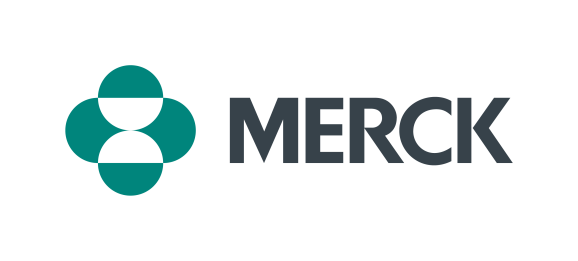
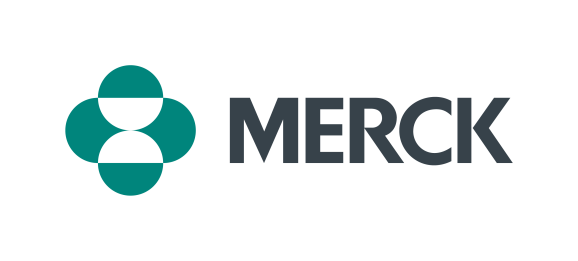
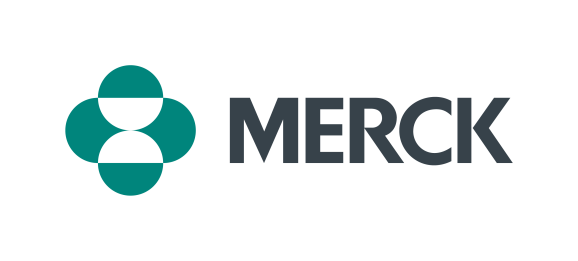
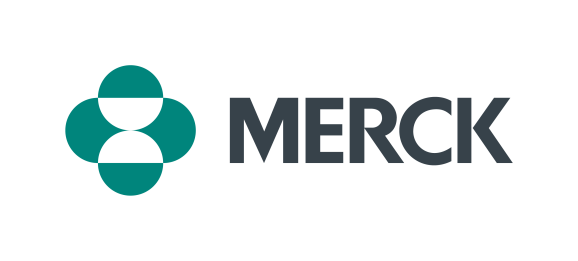
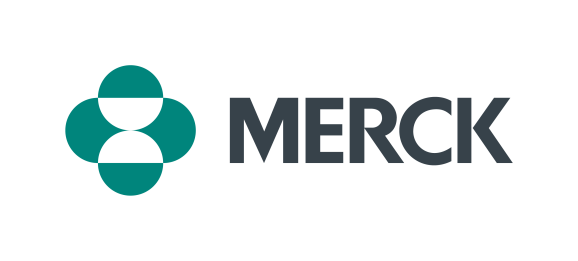
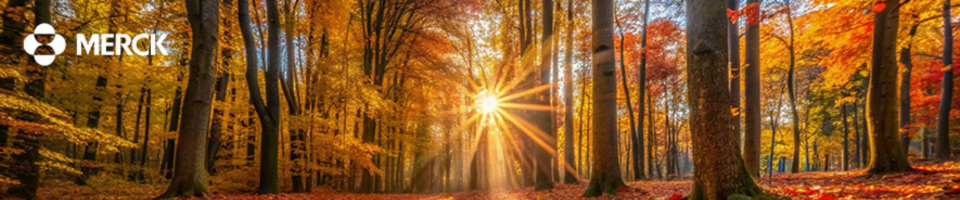
Job Description
The individual in this role must provide direction, coaching, and technical expertise to maintenance and instrumentation technicians assigned to start up and maintain the new facility (process, utility and automation assets). This individual must actively manage his/her team to reliably support customer demand (including employee development, routine coaching sessions, recognition, and performance management). Additionally, the selected individual must become proficient in the use of manufacturing systems and knowledgeable of site procedures to resolve process/equipment issues, minimize downtime, and ensure product quality. This role actively supports, participates, and embraces an inclusive team culture including significant interaction with Operations, Quality, Automation, Technology, and other groups as required.
Primary activities for this position will include, but not be limited to:
People Management / Leadership:
Provide leadership to the Maintenance team including coaching, development, and performance management.
Ensure a culture of inclusion and consistency is maintained, supporting positive employee relations at the shop floor level within the team and site.
Provide mentorship and training to team and peers.
Liaison effectively with alternate shifts, site Maintenance & Utilities, and Reliability Engineering teams to share best practices, deliver training, and ensure consistency and alignment in approach.
Actively participate on cross-functional teams in an inclusive manner to advance project goals and achieve deliverables.
Hire, develop, motivate, and manage a team to ensure reliable maintenance/calibration execution.
Assign yearly performance objectives and track metrics for the team in alignment with department and site goals
Provide leadership to the team as needed based on the team's capabilities and maturity
Ensure on time approval of payroll activities using site approved software like ADP.
Lead and support daily meetings to facilitate flow of information up/down through the organization
Hold regular team meetings to cascade information and collect team feedback
Provide clear consistent communication from shift to shift
Escalate issues as needed to ensure the right support/awareness is given to issues as they arise
Serve as a Subject Matter Expert during tours to provide area/process overview information to visitors/auditors upon request
Delivery :
Ensure that preventative and corrective maintenance support and calibrations to Clean Utilities, Purification, Fermentation, Sterile Supply and ALUM equipment is performed per schedule and/or business need.
Provide equipment related expertise and technical guidance necessary to troubleshoot and problem-solve equipment related issues to minimize impact to supply.
Manage adherence to departmental maintenance metrics; ensures adherence to design standards and downtime tracking.
Resolve and escalate issues impacting supply within the daily, weekly, and monthly IPT management processes.
Actively lead the daily Tier 1 Process and participate in the Tier 2, as required
Coach the team to ensure work orders and inventory transactions are complete, timely,and accurate
Manage team staffing and overtime to support customer demand while meeting budget targets
Recognize and communicate opportunities for cost savings
Interact with training vendor and coordinate training activities
Responsible for supporting:
Process Equipment (e.g. tanks/bioreactors, filtration skids, chromatography columns)
Support Equipment (e.g. washers, autoclaves, tube welders/sealers)
Process Utility Systems (e.g. Clean-In-Place (CIP) Systems, Water for Injection (WFI), and Clean Steam (CS))
Automated Systems (e.g. Distributed Control System (DCS), Programmable Logic Controllers (PLC), robotics)
Maintenance Equipment (e.g. tools and calibration equipment)
Compliance:
Ensure that maintenance activities are executed in compliance with Safety, Environmental and cGMP regulations.
Investigate, determine root cause, and implement robust CAPAs for any team related compliance discrepancies noted during day-to-day activities and/or audits. Escalate as per IPT management processes.
Ensure 100% PM compliance per maintenance schedule within team.
Participate in internal and external audits and inspections.
Continuous Improvement:
Provide a leadership presence on the manufacturing floor
Champion standard work to drive consistent use of best practices across teams
Regularly help the team troubleshoot issues to minimize downtime and maintain product quality
Represent maintenance and reliability input on project teams, as needed
Strong sponsor for the problem-solving efforts and solutions offered by other shifts and teams
Subject Matter expert for LOTO and permit writing for maintenance activities, Safety Management Information Systems (SMIS) transactions
Knowledge of mechanical/electrical maintenance and repair of mechanical, electrical and automated systems and equipment
Initiate SOP/PM/Calibration redlines and revisions
Shift and Schedule:
Successful candidate will be required to work a routine shift will be 2-2-3, 12-hour day shift schedule, including holidays and alternating weekends. Required to support an on-call schedule for off-day and weekends.
Education Minimum Requirement:
Bachelor's degree in Business, Science, or Engineering with four (4) years of relevant experience in manufacturing/ military service
OR
High School Diploma/GED with six (6) years of relevant experience in manufacturing/military service
Required Experience and Skills:
Minimum 4 years production/manufacturing experience, preferably in a cGMP environment
Demonstrate ability to lead a team
Maintenance experience; working maintenance knowledge of pharmaceutical processing, packaging, or utility equipment.
Demonstrated electro-mechanical troubleshooting and problem-solving skills with an understanding of maintenance processes, common equipment, and Computerized Maintenance Management Systems.
Demonstrated ability to work independently as a team leader and team member.
Demonstrated ability to motivate teams to achieve stretch goals and manage multiple priorities.
Demonstrated strong leadership and interpersonal skills with ability to coach, influence and support others through a culture of inclusion, feedback and empowerment.
Working knowledge of cGMPs and of regulatory requirements as they apply to the vaccine/pharmaceutical industry.
Ability to read and understand technical documents, drawings and specifications.
Proficiency using standard software including MS Excel, MS Word, etc.
Willing to work irregular hours to support multi-shift operation on an as needed basis.
Must be willing and able to lift 50 lbs., bend, stoop, squat, crawl, twist, climb ladders, and wear a respirator.
Preferred Experience and Skills:
Previous supervisory experience in a GMP-regulated manufacturing environment
Safety focus in daily work
Installation, operation, maintenance and/or troubleshooting experience with complex process and/or utility systems
Experience using electronic manufacturing systems (e.g. BMS, MES, SAP, Delta-V, etc.)
Experience in critical feedback and coaching, conflict resolution, performance management discussions
CMRP, CRL or similar Maintenance certification
Flexibility to perform various tasks to support the business.
Lean, Six Sigma, KATA problem solving skills
Ability to prioritize, align and simply to focus on and obtain business results
Previous training individuals in complex manufacturing/work environments
Meeting Facilitation/Training/Presentation Skills
Planning, Implementing, Directing, Control, Decision Making
#MSJR
Current Employees apply HERE
Current Contingent Workers apply HERE
US and Puerto Rico Residents Only:
Our company is committed to inclusion, ensuring that candidates can engage in a hiring process that exhibits their true capabilities. Please click here if you need an accommodation during the application or hiring process.
We are an Equal Opportunity Employer, committed to fostering an inclusive and diverse workplace. All qualified applicants will receive consideration for employment without regard to race, color, age, religion, sex, sexual orientation, gender identity, national origin, protected veteran status, or disability status, or other applicable legally protected characteristics. For more information about personal rights under the U.S. Equal Opportunity Employment laws, visit:
Pay Transparency Nondiscrimination
We are proud to be a company that embraces the value of bringing diverse, talented, and committed people together. The fastest way to breakthrough innovation is when diverse ideas come together in an inclusive environment. We encourage our colleagues to respectfully challenge one another's thinking and approach problems collectively.
Learn more about your rights, including under California, Colorado and other US State Acts
U.S. Hybrid Work Model
Effective September 5, 2023, employees in office-based positions in the U.S. will be working a Hybrid work consisting of three total days on-site per week, Monday - Thursday, although the specific days may vary by site or organization, with Friday designated as a remote-working day, unless business critical tasks require an on-site presence.This Hybrid work model does not apply to, and daily in-person attendance is required for, field-based positions; facility-based, manufacturing-based, or research-based positions where the work to be performed is located at a Company site; positions covered by a collective-bargaining agreement (unless the agreement provides for hybrid work); or any other position for which the Company has determined the job requirements cannot be reasonably met working remotely. Please note, this Hybrid work model guidance also does not apply to roles that have been designated as "remote".
San Francisco Residents Only:We will consider qualified applicants with arrest and conviction records for employment in compliance with the San Francisco Fair Chance Ordinance
Los Angeles Residents Only:We will consider for employment all qualified applicants, including those with criminal histories, in a manner consistent with the requirements of applicable state and local laws, including the City of Los Angeles' Fair Chance Initiative for Hiring Ordinance
Search Firm Representatives Please Read Carefully
Merck & Co., Inc., Rahway, NJ, USA, also known as Merck Sharp & Dohme LLC, Rahway, NJ, USA, does not accept unsolicited assistance from search firms for employment opportunities. All CVs / resumes submitted by search firms to any employee at our company without a valid written search agreement in place for this position will be deemed the sole property of our company. No fee will be paid in the event a candidate is hired by our company as a result of an agency referral where no pre-existing agreement is in place. Where agency agreements are in place, introductions are position specific. Please, no phone calls or emails.
Employee Status:
RegularRelocation:
DomesticVISA Sponsorship:
NoTravel Requirements:
10%Flexible Work Arrangements:
Not ApplicableShift:
1st - DayValid Driving License:
NoHazardous Material(s):
oils, high temperature bath,Job Posting End Date:
11/16/2024*A job posting is effective until 11:59:59PM on the day BEFOREthe listed job posting end date. Please ensure you apply to a job posting no later than the day BEFORE the job posting end date.
Requisition ID:R321402